蜗轮蜗杆设计优化技巧
蜗轮蜗杆传动设计的优化是一个复杂的过程,涉及多个方面,包括参数选择、材料选择、制造工艺、装配与调试等。以下是一些关键的优化技巧:
1. 参数优化
- 模数:选择合适的模数可以提高传动效率和承载能力。模数过大会导致结构笨重,模数过小则会增加制造难度和成本。
- 压力角:适当的压力角可以减少摩擦和磨损,提高传动效率。通常,压力角的选择范围在14.5°到20°之间。
- 齿数:合理的齿数选择可以优化传动比和承载能力。齿数过多会导致结构复杂,齿数过少则会影响传动的平稳性。
- 直径系数:直径系数的选择会影响蜗轮的尺寸和性能,合理选择可以提高传动效率和承载能力。
2. 材料选择
- 蜗轮材料:常用的蜗轮材料有铸铁、铜合金、铝合金等。选择时应考虑其耐磨性和耐腐蚀性。例如,铜合金具有良好的减摩性和耐磨性,适用于高负荷和高速传动。
- 蜗杆材料:常用的蜗杆材料有碳钢、合金钢、不锈钢等。选择时应考虑其强度和耐磨性。例如,合金钢具有较高的强度和耐磨性,适用于高负荷和高速传动。
- 高强度材料:选用高强度、耐磨性好的材料,如合金钢、陶瓷等,可以提高蜗轮蜗杆的使用寿命和机械性能。
3. 制造工艺
- 滚压加工:利用滚压工具对蜗杆表面进行滚压,可以提高表面质量和硬度。
- 切削加工:通过切削刀具对蜗杆进行切削,可以获得所需的形状和尺寸。
- 磨削加工:磨削加工可以提高蜗杆的表面光洁度和尺寸精度。
- 热处理:对蜗杆进行适当的热处理可以提高其硬度和耐磨性。
4. 装配与调试
- 调整中心距:通过调整中心距尺寸来尽量减少背隙,但需要考虑到蜗轮蜗杆制造公差、箱体中心距公差、热变形等问题。
- 预紧蜗轮:将两片蜗轮利用弹簧进行预紧,将被啮合的蜗杆齿夹紧在被预紧的蜗轮中间,从而消除背隙,但受限于弹簧的刚度,只能应用于轻载的场合。
- 双导程蜗杆:通过调整螺杆轴向的位移来实现背隙调整,KHK蜗杆被设计为轴向每移动1mm,背隙变化0.02mm。
- 凸轮滚子传动:通过径向预紧和优化滚子与蜗杆尺寸来实现零背隙的要求,并利用滚动摩擦替代滑动摩擦,实现高效率的大扭矩传动。
5. 设计优化与创新
- 引入润滑系统:设计有效的润滑系统,确保蜗杆在运转过程中得到充分润滑,降低磨损和摩擦阻力。
- 优化结构设计:在满足功能和强度要求的前提下,尽量减小蜗杆的尺寸和重量,提高设备的紧凑性。
- 提高传动效率:通过优化设计参数和材料选择,提高传动效率,减少能量损失和摩擦。
6. 维护与保养
- 定期润滑:按照设备要求定期对蜗杆进行润滑保养,保持其良好的工作状态。
- 更换磨损零件:对于磨损严重的零件及时进行更换,防止设备故障。
- 清洁与整理:保持蜗杆及其周围环境的清洁,定期进行清理和整理。
通过以上优化技巧,可以显著提高蜗轮蜗杆传动的性能和可靠性,延长其使用寿命,降低维护成本。
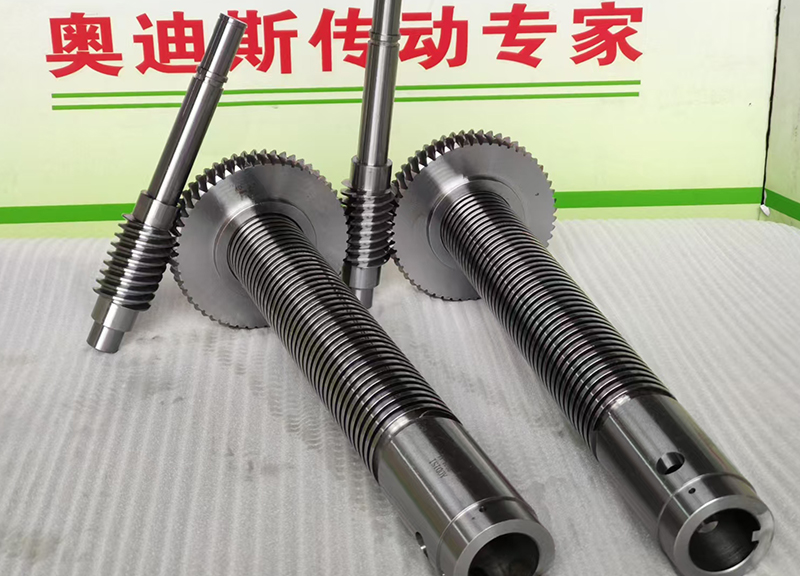
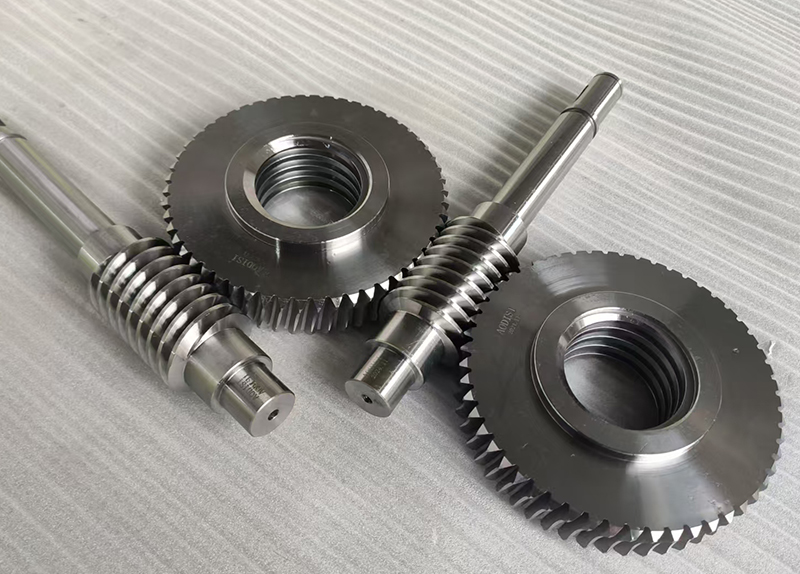
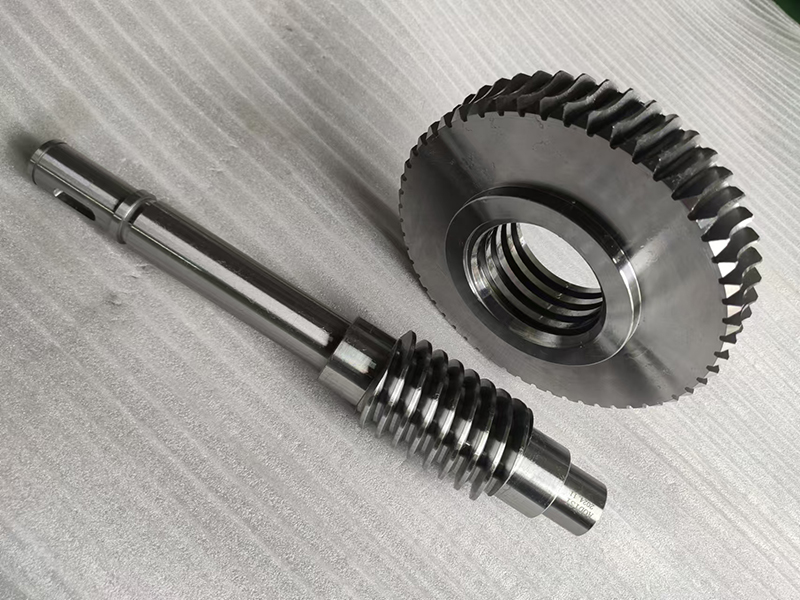